Austenitic Manganese Steel was discovered in 1882 by Robert Hadfield, who found that in quantities larger than 10%, Manganese is an Austenite stabiliser that renders steel fully austenitic at room temperature (after a suitable heat treatment).
This is highly significant in that Austenitic Manganese steel has the property of rapid work hardening, which is why it finds application in wear resistant and impact environments, such as cone, gyratory, jaw and impact crusher wear parts, as well as linings for semi-autogenous mills and shoes for draglines etc.
An initial hardness of ±215 BHN (in the range of Carbon steels and Ductile Irons) is obtained after heat-treatment by soaking the part at temperature above 1000°C and quenching rapidly in water, with superior impact toughness and mechanical properties. Work hardening, by impacting the surface of the part can more than double the surface hardness, resulting in a hard, wear-resistant layer.
This work hardening however can only occur once the yield strength (350-400 MPa) of the material is exceeded, i.e. the material must be deformed. Work hardening is also localised to the deformed zone (usually the surface), resulting in a hard wear resistant surface while maintaining a tough and ductile interior. The rate of work hardening is largely dependant on the Carbon content. However, higher Carbon content increases the risk of precipitating carbides during heat treatment, which weaken the material and increase the risk of cracking and may lead to failure of the part. This is also true of heavier sections, which cool more slowly during quenching. Several other alloying elements are used to improve the mechanical, work hardening and wear properties of Manganese steel.
Chromium, which was once a very popular alloying element, has very little effect on wear life, rate of work hardening etc. However, because of its strong carbide forming qualities, it increases the risk of carbide precipitation during heat treatment or welding, which adversely affects the performance of the part.
Molybdenum increases the yield strength and toughness of Manganese Steel. Due to the fact that Molybdenum has a higher affinity for Carbon than Iron, Manganese and Chromium, it forms Carbides preferentially to these other elements. The significance of this is the location of these Carbides within the metallic structure. Any cast metallic product, when viewed under a microscope, consists of many grains of metal separated by grain boundaries (see Figure 1 below). This can be simply symbolised as a brick wall, with the grains being the bricks and the grain boundaries being the cement. Now it can be seen that the strength of both these components is essential to create a strong wall. Hard Molybdenum Carbides form within the grain, improving the strength and hardness of the grain. Carbides of Iron, Manganese and Chromium tend to occur along the grain boundaries, weakening them. In addition, this makes these grades easier to produce, i.e. less cracking during thermal processing such as flame cutting and gouging, less chance of cracking during welding, either upgrading or reconditioning, and less chance of cracking during heat treatment.
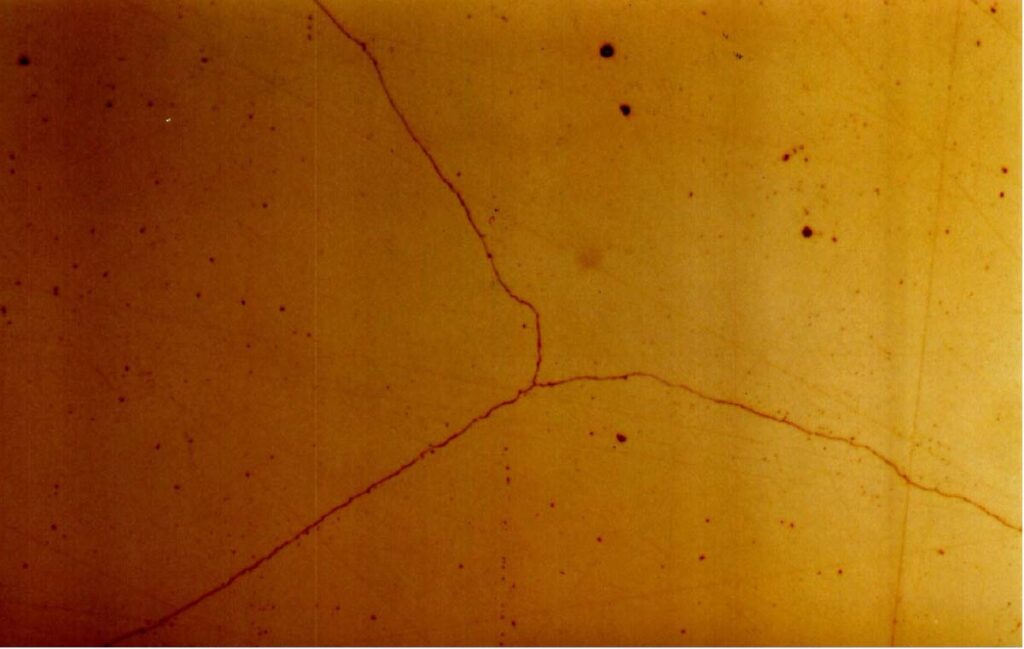
The single most significant drawback of work hardening materials is that of machinability, due to the fact that the material work hardens upon machining. For example, the high deformation which occurs upon drilling and tapping results in the Manganese steel hardening to such an extent that it exceeds that of the tool and results in high tool breakages. Turning and milling is possible with specific tooling, speeds and feed rates. These implications should always be considered in casting design.
In conclusion, Manganese Steel is a versatile and cost effective material for use in many applications where high mechanical and impact properties are required in conjunction with excellent wear-resistance.